What Is Ship Corrosion? A Beginner’s Guide To Understanding Marine Corrosion and Its Impact
In maritime environments, ship corrosion is a constant risk. Salt-laden sea spray and high salinity seawater create the perfect conditions for corrosion. But what exactly is corrosion? And how harmful can it be?
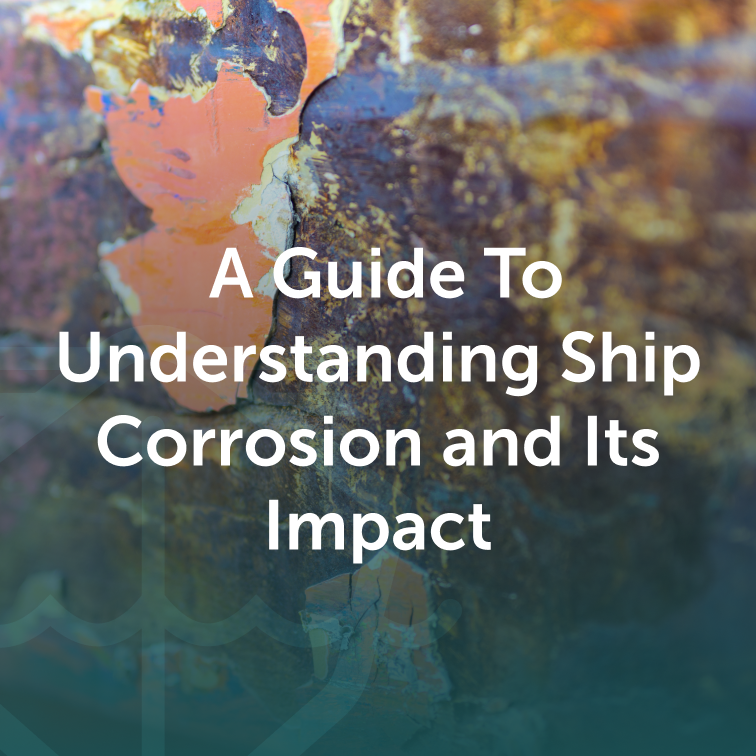
Corrosion is the degradation of a surface caused by chemical or electrochemical reactions with its environment. While it can occur on different materials, it is most commonly associated with metals. The reactions occur between the metal and the components in its environment, such as sulfur dioxide, oxygen, and water.
When metal disintegrates, it loses its structural integrity, making it weaker and more prone to failure. In ships, this could mean serious consequences, from reduced efficiency and costly repairs to catastrophic accidents. So, it’s important to understand how corrosion occurs and its effects. We cover them in detail below.
How Corrosion Occurs in Marine Environments
The corrosion process starts when a metal surface reacts with an environmental agent, such as water or oxygen. Salt or oxide films form on the metal’s surface in this reaction. Iron is an example. When exposed to oxygen and moisture, it forms iron oxide, commonly called rust.
Saltwater accelerates the corrosion mechanism in maritime environments since salt dissolves in water to form ions. These are highly conductive, promoting the metal’s reaction with oxygen and water. They act as “electrolytes” or “electron carriers,” facilitating electron transfer from the metal to oxygen. Due to this carrier effect, corrosion is relatively more aggressive in seawater than in freshwater.
At its core, corrosion is an electrochemical process that involves the following components:
Anode: The anode is the part of the metal where oxidation occurs and an electron is lost.
Cathode: Here, the reduction reaction (in which electrons are gained) occurs.
Electrolyte: An electrolyte is a medium that transfers ions between the anode and cathode. In our example, saltwater acts as an electrolyte.
Electrical Pathway: It’s the path through which the electrons move from the anode to the cathode, completing the electrochemical reaction. The metal itself provides this pathway.
The type of metal and its chemical composition significantly influence how quickly it corrodes. Some metals are highly reactive and corrode rapidly, while others are much more resistant.
Highly reactive metals like sodium and calcium readily react with water and oxygen, making them prone to corrosion. In contrast, less reactive metals like zinc react more slowly and typically only under specific conditions, such as in the presence of moisture or heat.
At the opposite end of the reactivity scale are the noble metals—gold, silver, platinum, and copper. These metals resist corrosion because they do not easily react with water or oxygen. This durability makes them ideal for use in jewelry, electronics, and decorative applications.
Atmospheric Corrosion vs. Immersed Corrosion
Atmospheric corrosion occurs on exposed surfaces of a ship or structure that are not continuously submerged in water — like the topside hull, superstructure, deck fittings, and masts. It is caused by moisture, oxygen, and airborne salts (from sea spray or ocean winds). It typically happens in cyclical wet and dry conditions, where condensation, rain, or splash deposits salts, and then the surface dries, creating an aggressive environment for corrosion.
Immersed corrosion (or marine immersion corrosion) refers to corrosion that occurs below the waterline, where the hull is fully submerged in seawater most of the time. This is what affects the underwater portion of the ship’s hull, propellers, rudders, sea chests, and similar components. This type is strongly driven by salinity, oxygen levels, temperature, and biofouling.
Types of Corrosion
The corrosion mechanisms differ across their types. These categories are based on the location and mode of corrosion. Here are some common types of corrosion.
Galvanic Corrosion
Galvanic corrosion or bimetallic corrosion is a process in which one metal corrodes in the presence of another. It occurs when two different metals are electrically connected and exposed to an electrolyte, like moisture. The more active metal (anode) corrodes faster, while the less active metal (cathode) remains intact.
The bow thruster tunnel is a common site for bimetallic corrosion due to the combination of dissimilar metals present in the area. Components like mild steel, stainless steel bands, and bronze elements such as the propeller or hub can create an electrochemical imbalance, accelerating localized corrosion and lead to pitting corrosion.
Pitting Corrosion
Pitting corrosion is a type of localized corrosion common in metals like iron, steel, and aluminum. It causes small pits to form on the surface, which can penetrate deep into the metal and cause structural damage.
The pit becomes the weak point where corrosive agents can quickly attack the metal. Although the damage continues deep within the metal, the surface only shows minor rust at the pit or cavity site.
Crevice Corrosion
A crevice is a small gap or space between two surfaces. Crevice corrosion occurs in tight spaces where oxygen and other corrosive agents cannot easily access them. It’s commonly found in areas with seals or joints, such as around bolts, gaskets, and fasteners.
A stagnant electrolyte solution, such as saltwater, can accumulate in these crevices. Initially, it doesn’t cause any problems. However, with time, oxygen depletion will occur, increasing the number of positive metal ions inside the crevice.
A differential aeration cell forms when the crevice’s interior becomes an anode and the surface outside becomes a cathode. In this cell, the anodic areas lack oxygen, while their cathodic counterparts have free oxygen access.
Negative ions then enter the crevice to balance the charge, causing an increase in acidity. The acidic environment further accelerates localized corrosion within the crevice.
Uniform Corrosion
As the name suggests, uniform corrosion occurs evenly over the entire surface. It’s the most common type of corrosion and can take various forms, such as rusting and tarnishing.
Uniform corrosion causes minimal pitting because it occurs throughout the metal surface. However, over time, the material loses mass, and its mechanical strength also gradually deteriorates.
The rate of uniform corrosion depends on the metal’s chemical composition and exposure to the corrosive environment. For example, steel will corrode faster in a saltwater solution than aluminum.
Stress Corrosion Cracking
As corrosion continues, cracks form in the metal over time. When combined with tensile stress (the force acting on a material that tries to stretch or elongate it), these cracks can grow and spread, causing significant damage. The process is called stress corrosion cracking.
It can consist of two types:
Intergranular: In this type of stress corrosion, cracks form along grain boundaries, which are weak areas in metals. It mainly affects high-strength alloys such as stainless steel and aluminum.
Transgranular: Cracks form within the grains of the metal in this type of stress corrosion cracking. It typically occurs in low-strength metals such as copper and brass.
Several environmental factors, such as temperature fluctuations, tensile stress, vibrations, and corrosive substances, can cause stress corrosion cracking. As the cracks progress, they can cause structural failure in ship hulls and other marine structures.
Environmental Conditions (pH, Temperature, Humidity, Salinity)
The main environmental conditions that impact the corrosion rate are as follows:
pH: The pH is a substance’s acidity or alkalinity. A lower pH means more acidic conditions, while a higher pH indicates an alkaline environment. Seawater has an average alkaline pH of 8.1, making it a corrosive environment for some metals.
Temperature: Higher temperatures increase the rate of corrosion, while lower temperatures slow it down because heat accelerates chemical reactions. Marine structures in warmer waters are more prone to corrosion than those in colder regions.
Humidity: The presence of humidity in the air can accelerate corrosion. High humidity levels, acting as an electrolyte, create a more corrosive environment for metals.
Salinity: The salt content in seawater significantly increases its conductivity. Salts dissociate into ions that facilitate the electrochemical reactions responsible for corrosion. This makes saltwater much more corrosive than freshwater. Areas with higher salinity, such as enclosed seas or tropical regions, tend to see faster metal degradation on ship hulls and offshore infrastructure.
Effects of Maritime Corrosion
Corrosion doesn’t only cause structural damage, but can also have economic and environmental impacts. For one, it deteriorates ship hulls and other marine structures, lowering their longevity and efficiency.
It can also make metals more susceptible to fatigue, rendering them unsafe for use. In fact, a study revealed that 90% of ship failures are due to corrosion.
According to a report by the National Association of Corrosion Engineers (NACE), corrosion costs the transportation industry $29.7 billion in loss, of which $2.7 billion is related to ships. These costs range from repairs and maintenance to replacement costs for corroded parts.
Marine Corrosion Prevention Strategies
While some corrosion prevention strategies are physical, such as coatings and inhibitors, others are more technical. Below, we discuss a few of them.
Choosing Corrosion-Resistant Materials
Using materials that are inherently resistant to corrosion is an effective method of preventing it. This approach is helpful in environments where exposure to corrosive elements is unavoidable.
Ship hull construction relies on a range of steel types, each selected for its specific structural properties and performance under marine conditions. According to Beamcut, the most commonly used steel grades are A, B, D, and E.
Grade A steel, a mild variety, is widely used in ship structures with thicknesses under 20 mm, such as bulkheads. Its popularity stems from its excellent weldability and cost-efficiency.
For areas that require slightly more strength, such as structures measuring between 20 mm and 25 mm, Grade B steel is typically employed.
Grade D steel is preferred for components exceeding 25 mm in thickness, offering enhanced crack resistance, which is vital for long-term structural integrity.
At the top of the strength spectrum is Grade E steel, which is heat-treated and used in high-stress areas like the ship’s keel, where structural demands are most intense.
Protective Coatings and Treatments
Antifouling coatings also help make metals less resistant to corrosion. These coatings form a barrier between the metal surface and corrosive elements, preventing direct contact.
Cathodic Protection
In cathodic production, dissimilar metals prevent corrosion, particularly in submerged structures like ships and offshore oil platforms. The more reactive metal acts as a sacrificial anode, corroding instead of the less reactive metal it is meant to protect.
A highly effective type of cathodic protection is the impressed current system, in which an external power source creates a continuous electrical current to protect the metal. Cathelco’s ICCP system is based on this principle. It allows prolonged protection against corrosion through the optimal placement and sizing of reference electrodes and MMO anodes.
Regular Maintenance and Inspection
Even with all these preventative measures, some degree of corrosion can occur. So, it’s imperative to inspect the condition of metal structures regularly. Underwater inspections can be carried out for ships and offshore platforms using remotely operated vehicles (ROVs) with cameras and sensors.
More importantly, you should periodically monitor the condition of coatings and cathodic protection. A regular maintenance cycle for metal structures and corrosion prevention strategies keep them in optimal condition and minimize costly repairs and replacements.
Frequently Asked Questions
What is corrosion in simple terms?
Corrosion is the deterioration of materials, mainly metal, caused by an electrochemical reaction with their environment. In this reaction, the material loses its structural and functional integrity.
Is corrosion just rust?
Rust is just one type of corrosion that occurs specifically on iron or steel. However, other metals and materials can also corrode in different ways, such as by tarnishing or pitting.
What is corrosion on a ship?
Corrosion is the formation of rust on a ship’s metal components, which can weaken and damage them over time. It may be caused by exposure to high salinity seawater and the operational profile of the ship.
What describes corrosion?
In chemistry, corrosion occurs when metals react with substances in their environment, leading to the gradual deterioration and loss of material from the metal surface.
Protecting Materials and Structures: The Importance of Ship Corrosion Prevention
As we’ve explained, corrosion causes monetary loss, safety hazards, and a reduction in operational efficiency. While it cannot be entirely stopped, measures can be taken to minimize its effects.
Corrosion prevention systems, such as the Cathelco Impressed Current Cathodic Protection System, can keep your maritime structures in excellent shape and increase their longevity. More importantly, you can save significantly on repair costs and downtime to keep your vessels in the water, where they belong. Get in touch with us to learn more about our ICCP systems.
Contact sales
Our expert team is here to guide you through our solutions tailored to your specific needs.
Systems, spares and service
- Corrosion Protection systems (ICCP systems)
- Marine Growth Prevention Systems (MGPS)
- Reverse Osmosis Desalinators (Cathelco Seafresh)
- Ultrasonic Antifouling Systems (USP DragGone™)