When Should Impressed Current Cathodic Protection Be Inspected? A Guide to Maintenance for Ships and Offshore Structures
Corrosion is a relentless issue for ships and offshore structures, leading to serious maintenance and financial burdens. Recent studies indicate that corrosion accounts for 3.4% of the global gross domestic product, with over 30% of this attributed to marine environments.
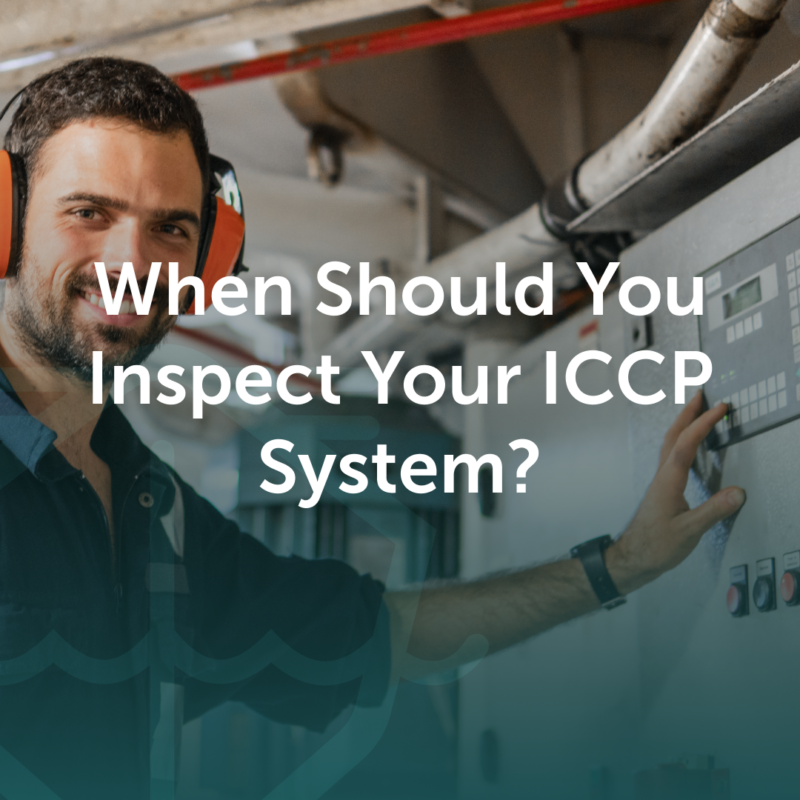
To combat this pervasive issue, many maritime operators use Impressed Current Cathodic Protection (ICCP) systems. These systems prevent corrosion by creating a continuous electrical current to the submerged metal surfaces. As a result, they inhibit the electrochemical reactions that cause corrosion.
However, ICCP systems won’t stay effective without regular inspections and maintenance. Neglecting these essential practices can lead to system failures, corrosion, and costly repairs. The question is, when should impressed current cathodic protection be inspected?
Overview of Impressed Current Cathodic Protection Systems
An Impressed Current Cathodic Protection (ICCP) system is designed to prevent corrosion in metal structures in marine environments. Unlike traditional systems, it does not rely on sacrificial anodes.
A typical ICCP system has three key components: anodes, a power source (usually a rectifier), and reference electrodes.
- The anodes are made from inert materials like titanium and coated with a mixed metal oxide. They’re strategically placed around the hull structure.
- The rectifier converts alternating current (AC) from the power grid into direct current (DC), supplying the necessary electrical flow.
- Reference electrodes monitor the system’s performance by measuring the electrical potential between the reference electrode and the structure.
These current systems are popular across many industries, including oil and gas, marine, and infrastructure. For instance, the maritime industry faces a massive financial burden due to corrosion, costing between $50 and $80 billion annually. Implementing ICCP systems is a cost-effective way to mitigate these expenses.
The Importance of Regular Inspections
Instead of just asking, “When should impressed current cathodic protection be inspected?” you may also be wondering why.
Regular inspections are important for maintaining the effectiveness of ICCP systems on ships and offshore structures. These systems are designed to prevent corrosion, but without routine checks, their performance can degrade. This leads to serious structural issues.
Over time, the anodes and reference electrodes can wear out or get damaged, compromising the system’s ability to protect the metal surfaces. Regular maintenance ensures that these metal components function correctly and safely.
Neglecting regular inspections can result in undetected corrosion issues, which reduce the effectiveness of the ICCP system and accelerate corrosion. Plus, electrical connectivity problems, like corroded or damaged connections, loose wiring, or broken cables, can interrupt the flow of current. This renders the system ineffective.
Additionally, there are significant financial implications of avoiding maintenance. Corrosion-related damage can lead to costly repairs and even catastrophic failures. Regular ICCP inspections allow you to find and address potential issues before they escalate.
In the long run, a proactive approach to maintenance not only preserves the structural integrity of marine assets but also ensures their operational efficiency.
How Often Should ICCP Systems Be Inspected?
The effectiveness of an ICCP system hinges on regular inspections. Without routine checks, corrosion can go unnoticed until it causes serious damage.
General Guidelines for Inspection Frequency
Here are some general guidelines on how often to inspect your ICCP systems:
- Initial Testing: ICCP systems must be tested by a qualified cathodic protection expert at the commissioning stage.
- Routine Inspections: After the initial testing, a full system inspection should take place at least once every three years, or yearly in some cases, as required by class bodies.
- Monthly Log Sheets: Monthly log sheets should be completed as part of routine system inspections. These checks help verify overall system integrity and functionality. By recording performance data consistently, minor issues can be identified early and addressed before they develop into major failures. Completed log sheets should be submitted to the system manufacturer for review and analysis, ensuring timely expert support and continuous system reliability.
- Detailed Yearly Inspections: A comprehensive inspection should be conducted annually by qualified personnel.
- Ongoing Monitoring: Rectifier output values (amps, volts) should be monitored daily. Any fluctuations may indicate a problem needing immediate attention.
Factors Influencing Maintenance Schedules
Environmental Conditions
Harsh environments can speed up corrosion, requiring more frequent inspections. Factors like high salinity, extreme temperatures, and strong currents can impact ICCP system performance. In such conditions, monthly checks become even more important.
System Age
Older cathodic protection systems, especially those installed over 10 years ago, may need closer monitoring due to potential wear and tear. Components degrade over time, and outdated systems might not function as well as newer ones.
Operational Changes
Any modifications to the cathodic protection system or the protected structure should prompt an immediate inspection. Changes such as hull modifications, new coatings, or additional electrical systems can affect ICCP performance.
3 Indicators Your ICCP System Needs Inspection
Even with a structured maintenance schedule, unexpected issues can arise. Recognizing early warning signs can save your vessel from costly repairs and system failures.
1. Performance Degradation
A drop in ICCP system performance is one of the clearest signs that an inspection is overdue. If voltage or current output levels fluctuate beyond expected ranges, it could indicate a failing anode, damaged wiring, or rectifier issues.
2. Changes in Environmental Conditions
Marine environments are unpredictable. Increased water salinity, temperature fluctuations, and sediment buildup can alter the electrical balance of the system.
3. System Malfunctions
ICCP systems are designed to operate with minimal intervention, but malfunctions do happen. If alarms are triggered, power supply inconsistencies appear, or components overheat, the system needs immediate attention.
Practical Advice for ICCP Inspections
Proper ICCP inspections include both routine visual assessments and detailed technical evaluations. Here are some key tips:
- Check the Anodes: While direct visual inspection of hull-mounted anodes is not feasible with the vessel afloat, routine checks should include inspection of anode cofferdams and electrical connections. Output tests should also be carried out to verify proper current distribution and system performance.
- Inspect Wiring and Connections: Loose, corroded, or damaged wiring can disrupt current flow. Ensure all connections are secure and oxidation-free.
- Monitor Output: Regularly check rectifier voltage and current readings. Drastic fluctuations may signal system or environmental issues.
- Evaluate Reference Electrodes: If readings are inconsistent, recalibration or replacement may be necessary.
- Perform a System Function Test: Conduct periodic tests to confirm that current is being properly distributed.
- Schedule Professional Inspections: Hire a corrosion specialist annually to comply with standards and maintain peak performance.
Invest in Lasting Protection: ICCP Systems with Lifetime Warranty
Regular inspections are key to keeping your ICCP system effective and your vessel or offshore structure safe from corrosion. Skipping checks can lead to costly damage, compliance issues, and a drop in operational efficiency.
Whether you need guidance on maintenance or a reliable ICCP solution, expert support makes all the difference. Learn more about advanced protection systems and how they can keep your structures safe by visiting Cathelco’s ICCP solutions.