Impressed Current Cathodic Protection: Benefits and uses
The maritime industry faces a massive financial burden due to corrosion. It costs the industry between $50 and $80 billion annually.
One powerful yet often undervalued solution is impressed current cathodic protection (ICCP). This system applies an electrical current to the structure, protecting it from the environment’s corrosive effects. Unlike galvanic cathodic protection like sacrificial anodes, impressed current cathodic protection can be more cost-effective in the long run.
In this guide, we’ll discuss what ICCP is, how it works, and its many benefits.
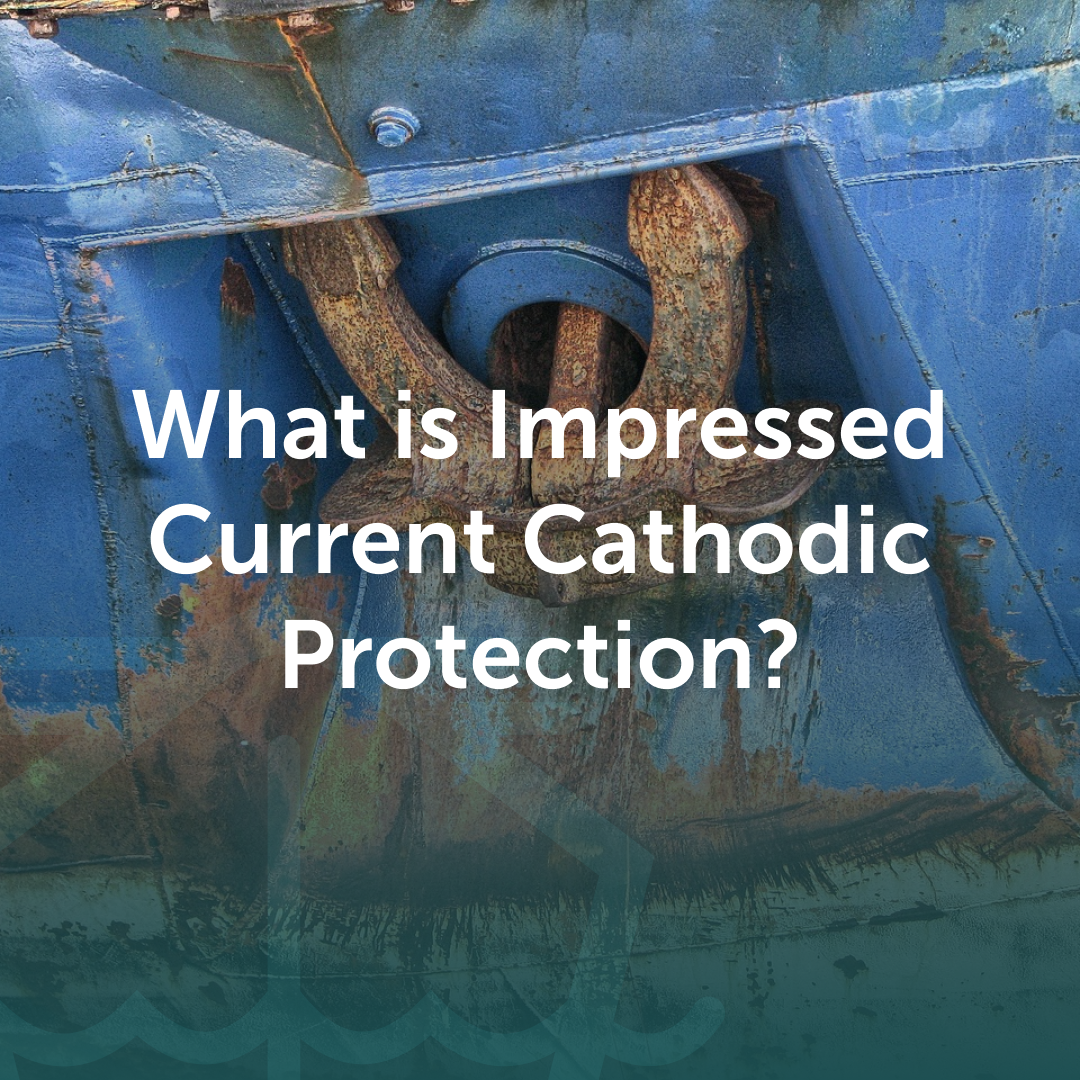
What is Impressed Current Cathodic Protection (ICCP)?
Impressed Current Cathodic Protection (ICCP) is a method used to prevent corrosion of metal structures by applying an external electrical current. This process counters the natural electrochemical reactions that cause corrosion.
Corrosion occurs when dissimilar metals, variations between hull plates and welds, or water aeration create anodic and cathodic sites on the structure. These sites form corrosion cells, where electric currents flow from the more reactive (anodic) site to the less reactive (cathodic) site, leading to metal degradation.
ICCP works by impressing an opposing electrical current onto the metal surface. This current is equal to or greater than the anodic currents driving the corrosion. By neutralizing these anodic currents, ICCP effectively protects the structure from corrosion.
In maritime environments, ICCP may be used for:
- Ship hulls, propellers, and other components
Corrosion is a major concern in the marine industry due to the presence of saltwater, which is highly corrosive. In fact, saltwater corrodes metal about five times faster than freshwater does.
ICCP prevents corrosion in these environments by providing a continuous and reliable protective current. That helps maintain the structural integrity of maritime assets.
How does Impressed Current Cathodic Protection work?
ICCP works by applying a direct current to the metal structure. This current suppresses naturally occurring anodic currents and therefore prevents corrosion. Key components of an ICCP system include:
- ICCP Anode: This is a titanium element coated in mixed metal oxide capable of delivering high current housed in an insulating material.
- Reference Electrode: This is a fixed reference cell, mainly Zinc, measuring the hull potential at the seawater interface.
- Power Supply: This device monitors the system performance and automatically provides the electrical current to drive the cathodic protection process.
The anode and reference electrode are mounted through the hull but are electrically insulated from the hull, and the power supply connects to both. When the power turns on, the reference cell measures the hull potential and is compared against a preset value which is suitable to prevent corrosion by delivering the correct amount of current, a current flows from the anode to the structure, impressing a current onto the surface suppressing anodic currents keeping the structure cathodic and protected. Finally, the control unit makes sure the ICCP is performing effectively.
ICCP vs. sacrificial anodes: Choosing the right corrosion protection
ICCP is a form of cathodic protection, but it differs from galvanic cathodic protection (Sacrificial Anodes). Both systems prevent corrosion by making the ship’s hull the cathode of an electrochemical cell, but they operate differently:
- Galvanic Cathodic Protection (GCP): Uses sacrificial anodes made of zinc, aluminum, or magnesium, which corrode instead of the hull.
- Impressed Current Cathodic Protection (ICCP): Uses an external power source to apply a controlled electrical current, preventing corrosion more efficiently and with less material consumption.
ICCP is often more effective for large vessels because it provides consistent protection without frequent anode replacements.
How to use Impressed Current Cathodic Protection?
If you’ve decided to utilize ICCP, the implementation isn’t too different from any other corrosion prevention method.
Here are the steps:
- First, evaluate your marine environment and structure to determine the appropriate anode, reference electrode and power supply requirements. For instance, a tropical or subtropical region with high salinity and temperatures may require a higher current demand than a polar region.
- Next, develop a detailed design plan. It should include the placement of anodes, power supply, control unit, and cables. You can adjust this plan as needed.
- Follow the design plan to install the ICCP system. You might need to hire a technician for proper grounding and cable routing.
However, the work doesn’t end with installation. You’ll need to monitor your ICCP system to ensure protection is being achieved. It’s also wise to monitor and replace the hull equipment if needed. Lastly, calibrate the control unit periodically to make sure the measurements are accurate.
If your ICCP is ineffective, it could be due to several reasons. The main reason is poorly maintained systems left uncalibrated.
It’s also possible that the anode and power supply placements need to be optimized. You can always revise your design plan with the help of an ICCP specialist.
Why use Impressed Current Cathodic Protection?
When protecting your valuable maritime assets, ICCP systems are often compared to sacrificial anodes (SA). While SAs are simple and effective, ICCP offers many more benefits as part of your long-term corrosion prevention strategy.
- Cost savings: ICCP allows you to monitor the hull potential for targeted current delivery. This way, there’s no unnecessary anode and power consumption, leading to fewer replacements and lower maintenance costs. Meanwhile, with SAs, there’s a constant current drain
- Scalability: ICCP systems can easily adapt to changing environmental conditions or the size of your protected structure. That means there’s no need for over-engineering or constant system upgrades. Since SAs are less scalable, the long-term costs can be hefty.
- Reliability: ICCP delivers a precise, controllable current. That means cathodic protection is consistent despite variations in the environment or structure size. It also performs better than SAs.
More importantly, ICCP is best for highly corrosive environments such as tropical waters or areas with heavy pollution. SAs can struggle to keep pace with the rapid corrosion rate.
Where to use Impressed Current Cathodic Protection?
ICCP is particularly effective in marine environments where saltwater corrosion is a major concern. It’s versatile enough to be applied to a wide range of marine structures. It’s used for the hulls, propellers, and underwater fittings of:
- Cargo ships
- Container ships
- Passenger ships
- Cruise ships
- Naval vessels
- Submarines
- Offshore supply vessels
- Fishing vessels
- Ferries
- Bulk carriers
- Research vessels
- Tugboats
- Yachts
How to select the right supplier for ICCP Systems
If you’ve chosen ICCP to protect your metal structures, the next step is to find a reliable ICCP supplier. The right supplier can help you get a good return on your investment, so choose wisely. Here are some factors to help you make an informed choice.
- Experience: Look for suppliers with specialized expertise in marine/offshore industries.
- Certifications: Verify that the supplier complies with standards such as ISO 9001, ISO 14001.
- Energy efficiency: The marine industry can harm the environment with its greenhouse gas emissions, ballast water releases, and more. You can offset some of it by opting for an energy-conscious and sustainable supplier.
- Customer support: Choose suppliers with global networks and responsive technical support. Quick responses to emergencies such as anode failures or power supply issues can make all the difference.
- Customized Solutions: Work with suppliers that are willing to manufacture customized solutions for your needs.
Questions to ask potential ICCP suppliers
- What is your experience in providing ICCP systems for a specific application (e.g., offshore platforms)?
- What certifications do your products comply with?
- Do you offer OEM spares and parts?
- What is your response time for technical support and maintenance requests?
- Do you have a global service network?
- What is your warranty policy for ICCP systems?
What you should remember
While other methods such as sacrificial anodes can be sufficient, ICCP is the best option for long-term corrosion prevention. Its upfront costs may be higher than that of sacrificial anodes, but it’s also more affordable, high-performing, and effective in the long run. If you’re ready to implement ICCP, reach out to a trusted supplier today.